The concept of the Digital Twin is increasingly entering the Water Sector as an innovation driver. More than ever, its role in bringing value to operators is being highlighted by industry professionals around the world.
What is a Digital Twin?
A Digital Twin is a computer model that virtually reflects and simulates a real object, its environment and interaction, providing a picture as accurate as possible of how that object behaves in real time.
This could be a water treatment plant, where the Digital Twin includes process models to simulate the treatment steps, physical assets (e.g. pumps) represented in CAD, and performance models to optimise resources (e.g. energy usage).
The Digital Twin is not a new disruptive technology. Rather, it is the natural evolution of technology trends over the last decade or more. For example:
- Online sensors are becoming cheaper and ubiquitous; the Internet of Things (IoT) provides connectivity
- Cloud computing is making vast, centralised computing resources inexpensive and accessible
- Advances in data analytics allows huge amounts of data to be processed for patterns and monitored for signals
- The increasing sophistication of 3D visualisation, computer-aided design (CAD) and graphics processing allows for unprecendented realism in computer-operator interactions
These technology trends are driving the water industry towards Digital Twins. The value is found in the direct cost savings related to decreased waste, increased efficiency and reduced downtime, and helping operators make better decisions faster.
Data-streams, decision-making and implementation in a Cyber-Physical System powered by a Digital Twin. © DHI
Types of models in a Digital Twin
The Digital Twin is a multi-model platform. In the water sector, a Digital Twin could include:
1. Water-process models – These may be physics-based or data-driven models. They may be forced by boundary conditions, such as weather predictions and other loads on the system.
2. An asset model – This is typically a 3D CAD model spatially related to a Geographic Information System (GIS). The asset model is a record of the physical assets and infrastructure. It is used to setup and configure the water process models.
3. Performance models – This type of model generates the benchmarks and metrics required for decision-making. It is often connected to the enterprise resource planning (ERP) software of the organisation, allowing, for example, automated scheduling of repairs and down-time.
All these models are digitally linked and updated in real-time. Together with the data analytics, they represent the complete Digital Twin. The sophistication of the models and their integration can grow with the digital maturity of the organisation. This is particularly true when physics-based and data-driven models are combined. In this case, the data-driven models can be used to teach and optimise the physics-based models. Such ‘Augmented Intelligence’ (AugI) can be used to enhance data management and control processes. For example, this is used in Model Predictive Control (MPC) approaches.
Bringing value
A Digital Twin creates transparency. It allows you to optimise processes and speed up operational decision-making. This brings increased effectivity and efficiency. The Digital Twin can provide a holistic understanding of a water system. It can be used for all manner of what-if scenarios and operator training. Essentially, all of this leads to better and faster data-driven decisions.
None of this is new. We have been building models into Decision Support Systems (DSS) for decades. The difference today is that the elements of the Digital Twin are linked to the real-world with the purpose of creating learning, autonomous systems. These links can be multi-directional, where sensors inform the models. The models make predictions that initiate a change of the system set-points. The loop is closed when the sensors detect the new system status influenced by actuators that is fed back to the models, and so on. In principle, this can be either fully automated, performed manually via a DSS, or more usually, a combination of the two.
Augmented Intelligence can be added to automate model recalibration, reconfiguration and self-optimisation of the Digital Twin. This enables a high degree of system autonomy for adapting quickly to changing environmental and operating conditions. This is when the physical and virtual worlds merge, creating a Cyber-Physical System.
Co-creating the Digital Twin ecosystem
The Digital Twin approach is not a ‘plug-in-ready’ product. It requires joint development and new alliances and partnerships. It opens new opportunities for the water sector. We invite early adopters to co-create and implement the full value-cycle with us. Visit the DHI website to find out more about our solutions and learn how this can help your water business.
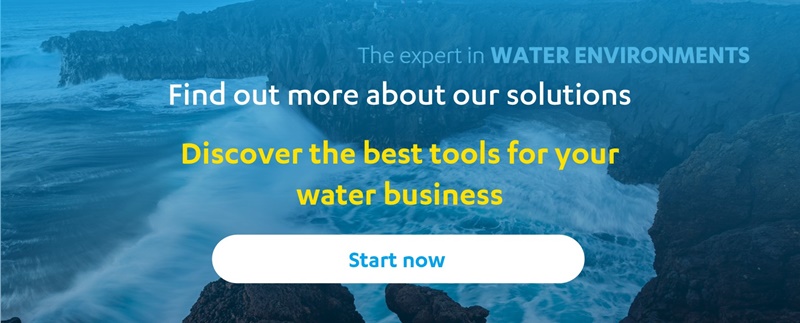